FACTORY MANAGER wanted: Salary R30 000 to R40 000 Per Month
Vacancy Details
Employer: West Coast Personnel
Benefits are 50% contribution to medical aid and a 7.5% company contribution to a provident fund.
Manufacturing experience is essential and chemical/mineral background would be highly advantageous.
You will be responsible for all production and warehousing and ensuring that the facility is well managed at the Plant. You will be responsible for coordinating the Quality, Environmental, Health, Safety, Legal Compliance programmes and related issues. You will also be responsible for ensuring that the business complies with all relevant SHEQ legislation, company policies and procedures, minimum requirements and permit requirements.
Qualifications and experience
Safety Management Qualification;
Production/Operations Management Certificate/Diploma;
5 years’ experience in managing a production line;
Intermediate to advanced MS Office knowledge;
Fluency in English;
Experience navigating and Utilising ERP;
Production/Manufacturing budgeting experience;
Literacy and numerical abilities to ensure that production can run effectively; and
Experience in Managing a staff.
Tasks related to the duties and responsibilities:
Schedule production and operational staff for the manufacturing of Products to ensure enough material is available to meet demand at all times;
Ensure that production planning is discussed with the Commercial Manager to incorporate customer demand outside daily budgeted production;
Ensure daily production schedules are fulfilled daily;
Implement and Maintain Production KPI’s to be presented to the Operations Director on a monthly basis;
Control and record production rates and meet or exceed target rates.
Ensure all product and packaging quality and standards are as per prescribed operating specifications;
Ensure all services and repairs for all equipment is conducted to ensure legislative compliance;
Develop, implement and maintain Machine Maintenance SOP’s to ensure optimal efficiency of production equipment;
Assist the Operations Director by contributing and motivating staff to contribute towards continuously improving the processes on site;
Assist and manage any issues after hours with staff on site when on Standby;
Manage all safety issues on site, attend Safety meetings and perform investigations;
Maintain, analyse and record production metricises with a focus on continuous improvement by:
Increasing production asset capacity and flexibility,
Reducing and minimizing wasteful expenditure, and
Ensuring required output is met in terms of QMS adherence and “On time, in full” shipping is maintained;
Align management style to the vision, values and strategy;
Positively practice and communicate values and ensure that employees understand what these are;
Manage people within the organisation through creating a culture of performance excellence;
Ensure that accurate job descriptions are communicated, detailing company expectations;
Identify areas of current and future personal development to ensure leadership excellence and continuous management development;
Manage the overall morale;
Select, train, motivate and evaluate staff and provide or co-ordinate staff training in conjunction with Human Resources;
Address poor performance constructively and timeously. Have a detailed discussion with the staff member to communicate the areas of poor performance and put measures in place to improve this;
Address misconduct and deviation from the values and Code of Conduct consistently through advice from HR;
Recruit in line with organisational needs as per the prescribed process;
Develop and manage succession plans for the organisation;
Ensure compliance with the Disciplinary Code; and
Address misconduct and deviation from the values consistently.
Ensure control of raw material and finished product stock levels;
Ensure that the existing processes are in being followed in receiving – monitoring the quality and quantity of the stock being receipted;
Storage of stock must promote efficient accessibility in a clean environment, taking into account the FIFO principal of moving stock;
Pay particular attention to the security of the stock in warehouses and implement adequate security procedures which support this;
Analyse the logistical arrangements, including timeliness, assessing the level of service provided, the quality of vehicles utilized and negotiating price improvements;
Manage stock levels including:
·
KPI
·
Variances
·
Adjustments
·
Efficiency of day to day trading
·
Price lists
Implement logistics and WH procedures which promote accurate record keeping and maintenance at national level;
Ensure that stock levels of all items pertaining to production are kept at prescribed operating levels to ensure that production can carry on at all times; and
Report and reduce national stock days to the level indicated by the board.
Ensure work stations and responsible areas are clean and tidy at all times.
Follow safe working practice as set out as per the Occupational Health and Safety Act (Hard Copy available on Site) in all tasks performed on site.
Coordinate SH committee meetings, and ensure that the attendance registers are signed, and records kept;
Conduct safety talks and toolbox talks with employees, highlighting matters of concern where necessary;
Ensure that there is continuous communication of safety issues;
Facilitate incident/accident investigations;
Do Hazard Identification, Risk Assessments, Hazard Analysis as well as environmental aspects and impact assessments;
Ensuring all employees comply with the necessary Personal Protection Equipment (PPE) requirements;
Ensure that all incidents are reported internally and externally in accordance with requirements;
Ensure appropriate signage is displayed in all branches ;
Ensure continuous improvement based on OSHAS & ISO standards;
Generally, support the development of a H&S culture in the company such that H&S becomes an established part of work being undertaken;
Ensure all staff is issued with, trained in the use of, and utilize relevant safety equipment
Ensure dangerous materials are stored and handled appropriately; and
Ensure regular risk assessments are undertaken, gaps identified, and relevant actions implemented.
Maintain the existing quality management system. i.e. ISO 9001;
Assist with implementation of control measures;
Ensure compliance with legislation;
Understand best practice in maintenance and improvement in quality;
Ensure relevant teams have training and manage quality management system;
Ensure that relevant processes are in place to support the quality and quantity of product as per customer specification; and
Ensure that systems and procedures are implemented to identify and respond to quality failures or reports.
Establish procedures and programmes to ensure operation within parameters of EM;
Ensure internal and external reporting of all requirements, incidents and deviations in accordance with regulations and EMP;
Develop a culture that incorporates environmental sustainability into all modes of operation;
Ensure internal and external reporting of all requirements, incidents and deviations in accordance with regulations and EMP;
Develop a culture that incorporates environmental sustainability into all modes of operation;
Work with relevant external suppliers to understand, measure, audit and report on current environmental impacts;
Identify regulatory gaps and implement measures to investigate and avoid; and
Identify opportunities for continuous improvement.
Email your CV to [email protected]
Apply before Tuesday, September 3, 2019 – 58 Days left
Companies may expire jobs at their own discretion.
If you have not received a response within two weeks, your application was most likely unsuccessful.
Apply Now
Source: Careers24
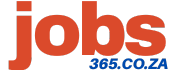